原価コラム

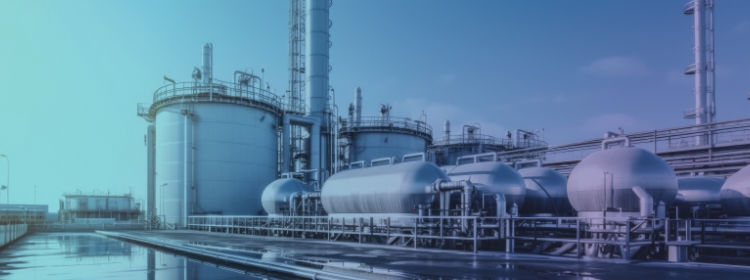
コスト削減、
何から手を付けたら良いか…

収益を改善するための方法として、売上を増やすこと・コストを削減することの2つがあります。
製造業においては、製造原価の比率が他業種よりも高い傾向があるため製造原価を削減することが収益改善に大きく寄与します。
しかしながら、闇雲にコスト削減策を実行しても、その成果が見えなかったり、場合によっては問題(人員削減による品質低下など)を引き起こしてしまう可能性もあります。
継続的な収益改善を実現するためには、原価管理が重要です。
原価管理=PDCAサイクルを
まわすこと
「PDCAサイクル」は、生産技術における品質管理など管理業務の改善に広く用いられている手法です。Plan(計画)→Do(実行)→Check(評価)→Action(改善)の4段階を繰り返していくことにより、業務を継続的に改善するという考え方です。原価管理は、以下のようなイメージでPDCAサイクルをまわすことにより収益改善を実現します。

最も重要な段階はCheck(差異分析)
PDCAサイクルのなかで最も重要な段階はCheck(差異分析)です。
原価差異分析は、標準原価(Plan)と実績原価(Do)との差がどんな要因で(価格差異、数量差異・・・)、どこで(工程、費目、製品、事業部・・・)発生しているかを把握・分析することにより改善へつなげることができます。
正しいActionへつながる分析のためには、まず正確な原価計算をおこない、その計算結果を様々な切り口で参照できることが必要となってきます。
J-CCOREsは、
差異分析のための機能が豊富です
原価管理システムJ-CCOREsは、充実した差異分析、予実対比機能をご用意しています。
部門別・費目別での原価差異分析や製品別での原価差異分析のほか、損益の差異分析も可能となっており、効果的な原価低減策の立案を支援します。
J-CCOREsは実績→計画→差異分析といった、業務運用レベルに応じて段階的にシステム導入していくことも可能です。
ぜひ、お気軽にお問合せください。
お問い合わせ
資料請求・デモンストレーション等、
お気軽にご相談下さい。